Printing with Reduced or Zero Alcohol Fount Solution
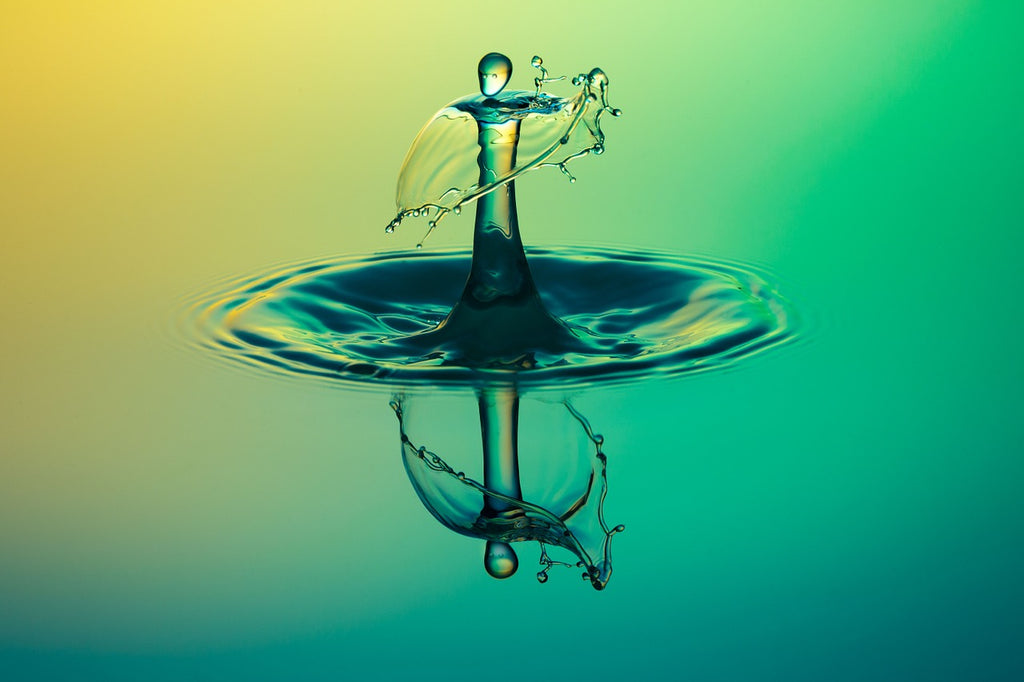
Improve profits by improving your environment
As the economic downturn bites harder printers are looking at saving costs wherever possible. Improvements to the environment are not an obvious place to look for savings but there are huge benefits in looking in this area.
Take a look in the pressroom at the consumables used and identify the most flammable and volatile material in use. Isopropanol Alcohol is a VOC (Volatile Organic Compound) that evaporates fast and has a flash point of only 12 degrees. You might also be surprised at how much you are spending on a product that just evaporates and pollutes our atmosphere.
So why do we use so much in the press damping system?
IPA added to the fountain solution will reduce the surface tension and make the water wetter and more efficient in dampening the plate. It will also increase the viscosity, and act as a disinfectant and anti foaming agent, that’s the only good news.
Bad news
- To use IPA correctly requires special handling and storage areas.
- It is expensive and will get more expensive.
- It forms the largest fire risk in the press room.
- It evaporates and often exceeds safe levels in the press room and requires constant replenishment.
- It dulls the colour and brightness of the printed job.
If IPA can be replaced by a safer non volatile alternative, costs can be saved whilst improving print quality and the environment. This is easier to achieve than most printers believe.
Alcohol has been reduced and replaced in many countries; Canada and the USA have probably the greatest experience and have legislation demanding it happens. European printers have identified the benefits and so have some governments who have applied high taxes or require a license be paid before IPA can be used.
So will the UK become alcohol free?
Alcohol free fountain solutions are available in the UK today. They have been formulated specifically for European conditions. Most press manufacturers have experience or are running them in showroom demonstrations.
To run alcohol free in commercial printers only requires knowledge and commitment.
Remember the effect of IPA, it reduces surface tension making the water wetter and increases viscosity, making it more viscous and easier to transport across the damping rollers.
Consider the chart below; it shows the surface tension and viscosity of a traditional fountains solution dosed at 3% without any IPA added.
Next add 5% IPA and note how the surface tension reduces and the viscosity increases.
Increase IPA to 10% and surface tension reduces still further whilst viscosity increases.
Surface Tension | Viscosity | ||
Dynes/Cm | Centistrokes | ||
3% Traditional Fountain Solution | 58 | 1.01 | |
Add 5% IPA | 47 | 1.18 | |
Add 10% IPA | 41 | 1.41 | |
Modern Alcohol Free Fount (at 5%) | 41 | 1.02 |
Now consider the same results with a modern alcohol free fountain solution and note that the surface tension is almost the same as adding 10% IPA but the viscosity is similar to having zero IPA.
To a printer this means the fountain solution is just as wet but not as thick. So in some cases metering rollers may have to be set a little lighter to allow the water through to the dampers.
When making the conversion, remember the objectives; to save money, improve safety, the environment, and improve print quality. That is worth investing a little time in a maintenance program before you start; e.g.
- Drain off the press chiller/recirculation and flush it with Prisco Royal Flush cleaner and disinfectant.
- Deep clean and condition the inking rollers using Prisco Eezy-Klene
- Remove calcium carbonate and other salt build-ups using Prisco Salt Remover. These are two separate operations and cannot be done with one product.
- Degrease chrome dampening rollers with Prisco Chrome Roller cleaner.
- Ink up the rollers and check the settings, some presses will benefit from reducing the roller stripes by 1 millimetre.
- When rollers are replaced further improvements can be achieved by using softer rollers, around 23 degrees shore. New technology in roller compounds also makes hydrophilic rollers available.
Modern presses run well without very much tuning; even older presses can be run with very little alcohol by employing the same technology.
Some times, during a conversion a problem does occur, typically on one unit when all others are printing fine. Remember what’s needed; knowledge and commitment.
If one unit has a problem when all others are printing its not because the alcohol has been removed, it’s a problem unique to that unit. The printer is aware but the temptation not to reach for IPA needs commitment.
Press conditions vary greatly and a fountain solution has to compliment the plates, ink and rollers being used. Ink and Print have a range of reduced and alcohol free fountain solutions so it may be worth trying more than one product to achieve the best result. Ink and Print will also be able to help with accurate control of fountain solution on press and be able to advise on the best dosage together with the resulting pH and conductivity readings.
For more information on this topic please contact Andrea Brooke 01293 532086, or andrea@inkandprint.com
Need to replenish your Process Ink or Litho Print Supplies?
We supply a full range of Print Consumables, including Van Son Process Inks, Standard Pantone Ink, Pantone Matching Guides, Litho Print Chemistry, Litho Printing Blankets and OverPrint Varnishes.
- Clive Harper